OYKA redefines quality with Valmet IQ Quality Control System
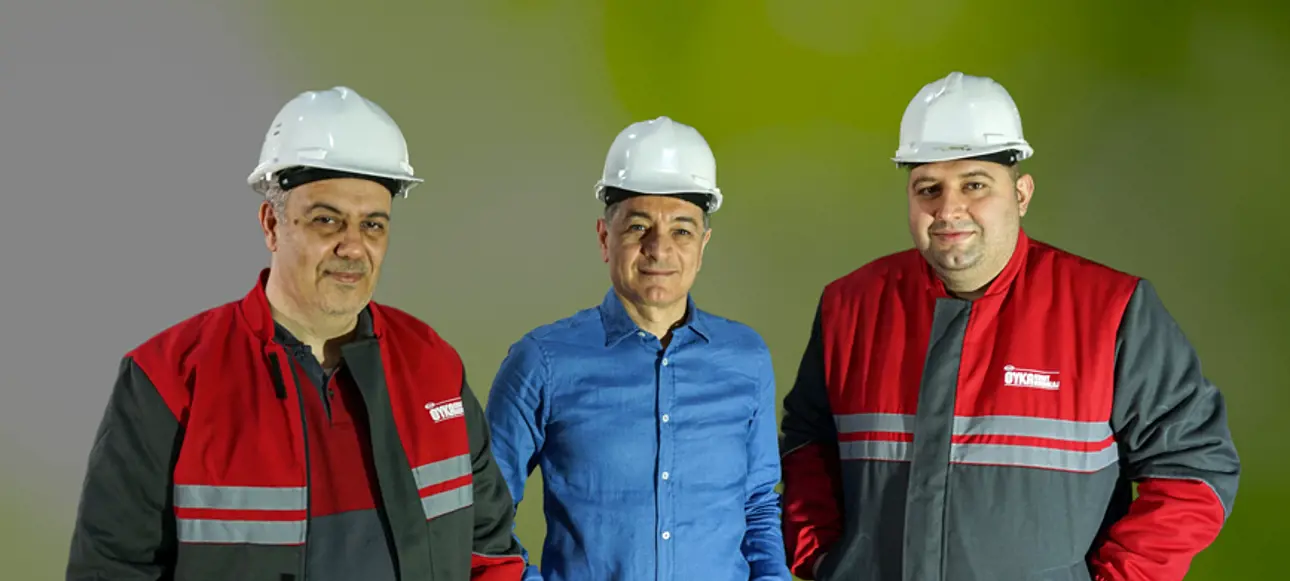
When OYKA, the only integrated pulp and kraft paper manufacturer in Turkey, decided to replace its aging quality control system (QCS), the team knew exactly what they needed. But what began as a targeted system upgrade with Valmet in 2022 quickly evolved into a comprehensive transformation of the production process.
We were expecting a 50% improvement, but the results were incredible, and we achieved around 100–110% improvement specifically in 2-sigma moisture values.”
Founded in 1963 under SEKA and privatized in 2003, OYKA’s Çaycuma mill operates a robust Fourdrinier line with an annual capacity of 100,000 tons. From wood chipping and pulp cooking to paper production and recovery, the mill functions as a fully integrated facility.
By the early 2020s, however, the quality control system, originally installed in 1995, was no longer meeting modern production demands. Customers expected tighter tolerances and greater consistency.
“Quality has always been a priority,” says Paper Production Manager Özgür Barış Özdemir. “But the way we controlled it was no longer enough. Basis weight and moisture were fluctuating beyond acceptable limits, and we were constantly putting out fires.”
Bilge adds, “The old system masked the actual variances with filters. Once we saw the real data, we understood the scale of the challenge.”
From system replacement to full process transformation
After evaluating several providers in 2021, OYKA chose Valmet as its quality control partner. What followed was more than just a system replacement. It was a hands-on, co-engineered project based on mutual understanding.
“If we had simply asked for a quality control system, we would not have achieved this level of success,” says Özdemir. “We had a clear vision, and Valmet aligned with it from the start.”
Commissioned in March 2022 with just three days of planned downtime, the project included more than equipment. Along with new-generation positioned at the Klupak and reel locations, OYKA adopted key process-enhancing technologies. The manufacturer also automated several manual operations.
“We were deeply involved in shaping the configuration,” says Bilge. “We moved beyond just monitoring values to having the system control the process in real time. That made all the difference.”
Reliable measurements and stable production
The impact of the Valmet IQ QCS was both immediate and measurable. Where previous 2-sigma deviations in basis weight had ranged from 2 to 4 g/m², the new system reduced this to just 1 to 1.5 g/m², validated by OYKA’s own laboratory tests.
The 2-sigma values practically melted before our eyes. This level of stability is nearly flawless in our industry.”
The most significant improvement was observed in the 2-sigma moisture values.
The system’s optimization extended far beyond measurement. “Machine downtimes and paper breaks decreased, speed improved, and production output increased by around 10%,” says Bilge.
Energy efficiency also saw a major boost, with steam savings of 0.3 tons per ton of paper, equivalent to 3-3,5 tons per hour. “The payback period was just three to four months,” he adds.
Customers noticed the updates, too. “The change was so apparent that they started telling us, ‘Your paper is different, quality has improved.’ Even we didn’t expect to hear it so clearly,” says Özdemir.
Continued collaboration from setup to long-term success
A major reason for the project's success was Valmet’s local and international support. Coordinated by Hamit Demir, Valmet’s Turkey Sales Manager, the deployment team worked closely with OYKA, both remotely and on-site.
“Valmet’s technology is excellent, but the person commissioning the system is very important. Hamit wasn’t just a Valmet representative, he also worked as a part of our team to achieve success,” says Özdemir. “He helped translate our needs to the global team and we customized the system together step by step.”
The collaboration continued after launching the system. A Valmet engineer delivered on-site fine-tuning and training that enabled OYKA to create its own operating manual for the system. “Now, our maintenance team knows exactly what to do. We even have a handbook to follow every detail,” says Bilge.
Valmet QCS is no longer just a quality control system. It’s the heart of our production.”
The Valmet IQ QCS exceeded expectations not only in measurement accuracy and process stability, but also in its remarkably low maintenance needs. Apart from routine annual servicing, no major interventions have been required. “A few technical support needs after installation were quickly resolved via Valmet’s remote connection feature. This reliability is critical for us,” Özdemir emphasizes.
The success of the Valmet IQ QCS project paved the way for OYKA’s next major upgrade: the Valmet Cellulose Fiber Analyzer. “The data and insights from the QCS gave us the confidence to move forward. We didn’t even consider alternative vendors,” says Özdemir.
OYKA’s Technical Services Manager, Hasan Hüseyin Seren, sums up the project’s success: “Valmet QCS is no longer just a quality control system. It’s the heart of our production. It’s reduced customer complaints, stabilized our processes, and given us a clear path forward. Thanks to the training and support we received, we now know how to take care of this system. Our next task is to maintain it well and make it work for us every day, as it continues to provide great advantages.”