Umka Board Mill increases capacity by 70 percent with three rebuilds
Umka Board Mill invested in three large rebuild projects, selecting Valmet as the main supplier. The rebuilds increased their capacity by nearly 70 percent and significantly improved board quality. As a result, Umka now meets the market’s demanding expectations and is attracting new business and customers.
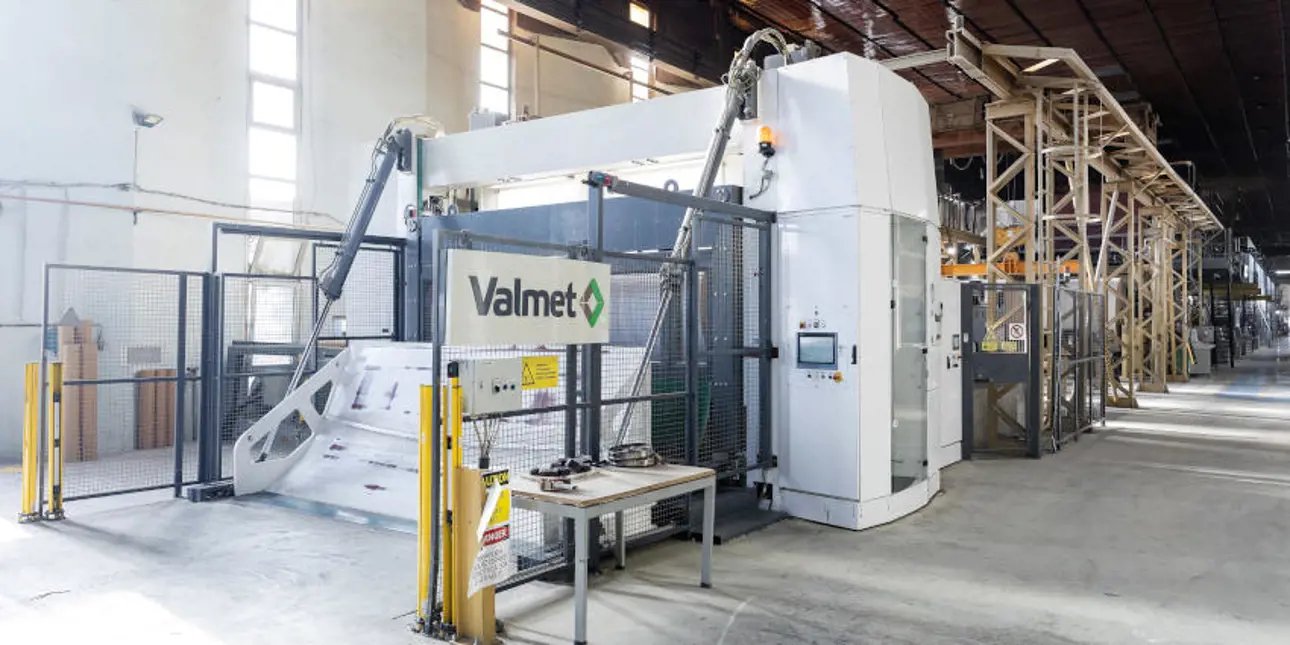
Investing in the future
Umka Board Mill is a family-owned business and a member of Kappa Star group, with a long history in paper making. Located in Umka, Serbia, the mill currently produces 220,000 tonnes of recycled coated white lined chipboard annually, with a basis weight range of 210–450 grams per square meter. They utilize an equal amount of recycled paper from the total output. Seventy percent of the board is used in the food packaging sector, while the remaining thirty percent serves the pharmaceutical, hygiene product, automotive, and toy industries.
In 2019, Umka was at a crossroads, with two options. They could continue as before, with old technology and an annual production capacity of 130,000 tonnes. Or they could invest in new technology, increase capacity, and open new markets. Umka chose the latter and started to look for solutions.
The investments began with the main goal to increase capacity and enhance the quality of the board. Valmet was chosen as the main supplier for three major rebuild projects. In addition to the investments, both commercial and operational efficiency were improved internally.
Umka increased the capacity by almost 70 percent.
“Just a month after the first rebuild, we achieved the best results in Umka’s history. And four years later, Umka increased the capacity by almost 70 percent,” says Saša Dobrić, Operations Director at Umka Board Mill.
“We can now serve more than 40 different European markets. We’ve increased the cooperation with our existing customers and opened new projects with them. We’ve also gained new customers, new markets, and new niches,” says Nikola Pejović, General Manager at Umka Board Mill.
Nikola Pejović, General Manager at Umka Board Mill. |
|
Saša Dobrić, Operations Director at Umka Board Mill. |
Three large rebuild projects
The first and largest project started up in 2021, in the middle of the Covid pandemic. The biggest changes were three new headboxes, a hybrid forming section with multiple fourdriniers, a new curtain coater, and a new winder.
“We were guided by the principle that the potential supplier must meet our requirements, both in providing the best possible technology and being reliable – not only during the project phase, but in the coming years and decades,” Dobrić explains.
Covid restrictions challenged the project from the outset. All the meetings in the engineering phase and even the Factory Acceptance Test (FAT) were organized online.
The reconstruction itself was done within 90 days exactly as planned, without a single day of delay.
“At the end of the day, we managed to proceed and prepare everything on time. The reconstruction itself was done within 90 days exactly as planned, without a single day of delay,” says Dobrić. “The second jumbo reel produced was already the sellable product.”
Based on the positive experiences, from negotiations to the engineering, start-up, and optimization phases, Umka decided to continue the cooperation with Valmet in the next two projects. In 2023, a completely new OCC line was started up, and seven new coating air dryers were installed in 2024.
Enhancing efficiency and stock quality with the OCC line
The new OCC line, with a capacity of 600 tonnes of bone-dry material per day, has significantly improved production efficiency and stock quality. The advanced screening technology with 0.15 mm slot baskets ensures exceptionally clean stock by removing impurities effectively.
“The OCC line is proven technology, and it’s really adjustable throughout the process. Our best experience is with the low-consistency cleaner plant, where we heavily discharge all the sand from the stock, which is very beneficial for all the rotors and baskets, but also for all the machinery that comes after this plant,” Uroš Mančić, Production Director at Umka Board Mill. “We’re proud to say we’ve completely combined stock preparation and the machine’s wet end from one supplier.”
Further improvements were achieved when Valmet upgraded the DIP line with new fine and coarse screening systems and a completely new cleaner plant.
The new OCC line significantly improved stock quality.
Key paper technologies improve quality further
The wet end consists of three state-of-the-art OptiFlo Fourdrinier headboxes that have improved the machine’s stability, runnability and board quality remarkably. “The main benefit of the headboxes is the CD profiling. Previously, the basis weight profile 2-sigma values were from three to five grams per square meter. Now, they’re only up to 1.5. We achieved this with Valmet dilution profiling equipment on the filler ply,” says Mančić.
The first rebuild delivery included major changes in the wet end.
A new and highly automated OptiCoat Layer curtain coating station replaced an old air knife. “It evenly distributes the coating across the width of the web,” says Mančić. “It’s also reduced the web breaks on this part of the machine by up to 30 percent.”
In the latest rebuild, the old air dryers and infrared dryers were replaced by new OptiDry Coat coating air dryers. Even though the technology is still new for Umka, they have been able to speed up the machine. It also increases runnability stability and the security of the machine by reducing the risk of fires.
A new winder was the starting point of all the investments when Umka wanted to increase capacity significantly. “We were seeking a completely automated machine that would offer the best performance and runnability,” says Mančić. “We recognized Valmet’s OptiWin Drum two-drum winder as the best possible solution on the market.”
Fast start-up with automation
To achieve Umka’s targets, Valmet delivered the Valmet DNA Automation System with Valmet Performance Center. Umka has been very satisfied with the new automation systems – even if the changes prompted some initial suspicion.
“As the automation manager, I was strongly opposed to acquiring a new automation system for our mill during the project’s negotiation phase – I was mostly concerned about how it would interconnect with our existing systems,” says Miloš Stanković, Project Manager at Umka Board Mill. “But during the start-up phase, I was glad we’d listened to Valmet’s suggestion of acquiring and installing Valmet DNA because it gave us the fastest start-up we could have expected for such a large board machine rebuild.”
Stanković is particularly pleased that all the Valmet DNA data displays can be reviewed historically, showing the values as they were at the time. The system has been reliable, and any improvement ideas for the system have been implemented quickly. According to Umka, Valmet’s support during and after the start-up has been at a high level.
Uroš Mančić, Production Director at Umka Board Mill. |
|
Miloš Stanković, Project Manager at Umka Board Mill. |
High quality and good cooperation
All three rebuilds met the investment targets. Umka increased annual production capacity from 130,000 to 220,000 tonnes and significantly improved board quality.
“Our final board has much better printing properties. With this level of quality, we can meet the very demanding expectations of the market and our customers all over Europe,” Dobrić says. “The decision to partner with Valmet on such a big project was the right call for us, and we’re really looking forward to cooperating more in the future,” he adds.
Saša Dobrić, Operations Director at Umka Board Mill and Riikka Antikainen, Director, Marketing & Product Sales inspecting the quality of the produced board.
Text Salla Aalto
Photos North Arrow Films
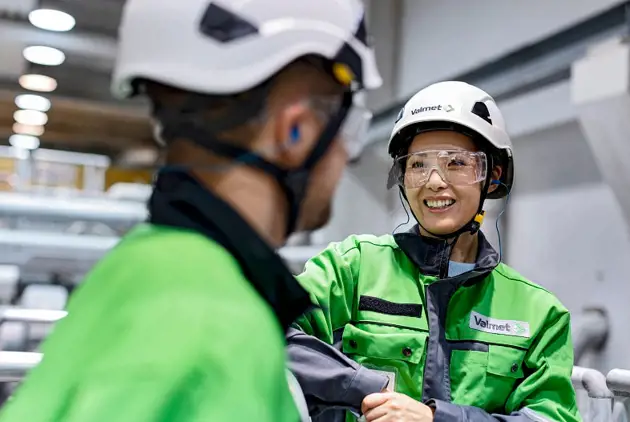
Want to talk to our board & paper experts?
If you wish to get further information like technical specifications or details, need a quotation, or wish to discuss different solutions, fill in the contact form and our experts will contact you shortly.
Contact our experts