Future-proofing valve control
New distributed control systems (DCSs) reduce operating expenses in a range of cement production processes, including the operation and maintenance costs of valves. Valmet explains the importance of DCSs and highlights advances in valve and pump technology
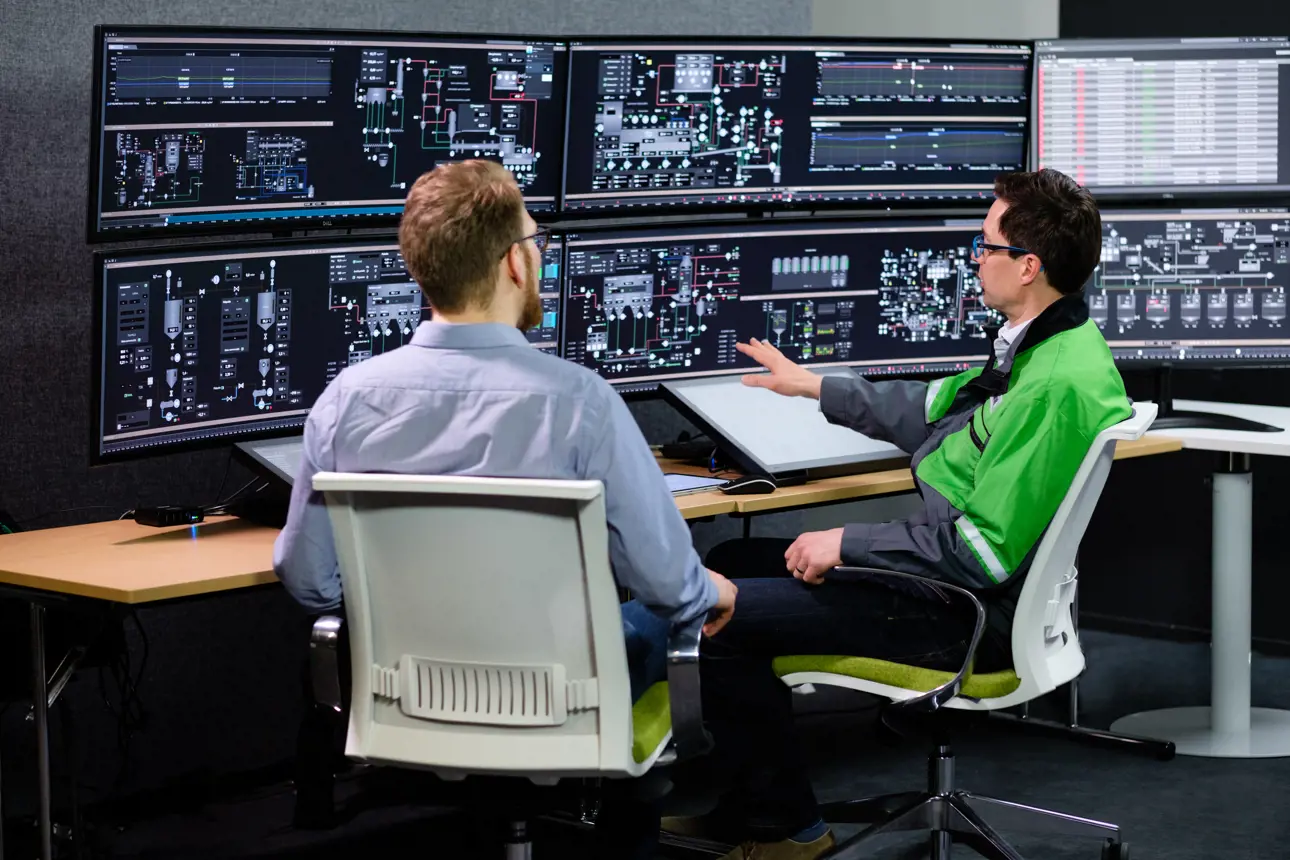
A futuristic DCS system can perform advanced plant or kiln management. These newer systems can be web based so users of all types can access plant performance and issues anytime or anywhere.
New future-proof distributed control systems (DCSs) are designed to meet a cement plant’s process automation requirements. These systems combine all controls for various aspects of cement production, including process, equipment, quality, supervisory, drive, optimisation, and mechanical condition monitoring requirements into a single platform. They can adapt seamlessly to different operational needs, ensuring scalability for the plant’s diverse requirements.A DCS can prioritise reliability, providing consistent and stable operations within the cement industry. It utilises a user-friendly interface, DNA UI, and offers intuitive tools for all user levels from control room operators to corporate management, facilitating effective monitoring of and interaction with the production process. The DNA UI uses web-based technology, therefore giving excellent access to all office and tablet users. Moreover, new DNA DCS architecture can be designed to meet a range of requirements, including:
• high system reliability, thanks to proven system components
• flexible usage, achieved by operational functionality in various locations
• sophisticated analysis and reporting needs
• advanced control tasks and algorithms.
DCS Requirements
DCSs should be scalable multiuser environments for concurrent engineering. They allow life cycle management for all control applications, field buses and field devices, as well as network document management. In addition, advanced diagnostic tools offer easy maintenance support for both applications and hardware.
DCS Security
Security of a DCS must be top priority.The DCS should follow defense-in-depth practices, with antivirus protection for Windows-based nodes, a secure network architecture with a demilitarised zone between the office network and system, and alignment with industry cybersecurity standards, ensuring the safeguarding of critical production automation systems.
Advanced applications
Ideally the DCS should offer a suite of advanced applications which offer real-time insights, predictive analysis, and actionable recommendations, ensuring peak operation, minimising downtime and maintenance costs.
Two advanced applications suitable for the cement industry which can be offered stand alone or with the DCS are a visible thermal imaging system and control loop optimization software. A visible thermal imaging system includes a rugged, air-cooled, HD visible camera paired with a high-resolution thermal sensor for real-time product temperature measurements. Designed for comprehensive observation and analysis of kiln environments, the visible thermal imaging system provides unparalleled image quality from start-up to full-load conditions.
A control loop optimization software, such as Valmet’s PlantTriage, continuously monitors industrial plants, identifies issues, prioritizes them based on technical and economic factors, offers root cause analysis, and provides analysis tools, including an embedded PID tuning feature, for efficient issue resolution.
Reducing operating expence in dense phase systems
Cement plants continuously deal with high operating and maintenance costs of dense phase systems. Therefore, alternatives that reduce operating expense as well as maintenance and downtime are required. Certain valve designs can help to achieve these objectives. Some of the common types include knife gate valves, switching valves and butterfly valves. In addition, a valve type that is gaining popularity is the high-quality pinch valve.
In dense phase systems a valve that has restrictions or metal components such as flappers or discs in the pipe stream is subject to extreme wear. Even a knife gate blade with the smallest bit of leakage quicky turns into high leakage due to the high velocity abrasive wear that dry cement creates. Over time the ends of the blades or flappers start to look like a shark’s mouth with jagged edges from the wear. These require high-cost maintenance and repair. A better solution is a valve that has no pockets or cavities for dry cement to migrate into. Also, a valve that is 100 per cent full port when in the open position is a must to keep velocities and wear low. A pinch valve meets these criteria. When the valve is fully open it is literally an extension of the pipe with a 100 per cent full bore hole through the centre of the valve. The only part in contact with the medium is a rubber sleeve that is the exact diameter of the pipeline it is installed within. When the valve is closed it is fully bubble tight and eliminates velocity wear. Many cement plants utilise rubber-lined piping and understand the abrasion-resistant properties of rubber.
The valve should also close equally from the top and bottom and meet in the centreline of the pipeline when closed. Closing from both sides helps reduce stress from overstretching the rubber sleeve in a pinch valve. In many cases, a high-quality pinch valve helps reduce operational expenditure significantly when compared to other valve types in a dense phase system. The repair of a pinch valve is low cost and can be carried out on site with a replacement rubber sleeve without the need for any special tools or extensive training for the maintenance team. Finally, a high-quality valve with an enclosed screw mechanism is always easy to operate for maintenance teams.
Grinding agent delivery
A plug-and-play three-pump system at a cement plant: delivered, tested and operational
The delivery of grinding agent can be improved to reduce operating cost, and reduce time to reprime pumps and reprogramming of pumps by selecting better pumping technologies such as peristaltic pumps.
A peristaltic pump has the following advantages:
• it can run dry without damage.
• it can both perform suction lift duties and deliver higher pressures than some alternative pumps used in cement plants.
• a peristaltic pump can pump slurries with as high as 80 per cent solids.
• it can reverse direction.
• in most cases the only repair component is a plastic tube assembly or a rubber hose.
• peristaltic pumps may be capable of 5000:1 turndown, which provides
immense accuracy in delivery of expensive chemicals.
Peristaltic pumps have gained in popularity due to their reliability as well as their simplicity and ease of repair with smaller assemblies being replaced in 1-2min.
Plug and play
Any cement customers purchase a packaged pump system rather than stand-alone pumps. Many cement plants require multiple peristaltic pumps and these pumps can be assembled on a skid with auxiliaries such as pulsation dampeners, pressure relief valves, safety shut-off valves and gauges. All equipment is mounted in a pre-designed safe and effective environment for the pumps. The entire skid package can be delivered to the cement plant with a factory acceptance test performed. The entire package is plug and play, only requiring electrical connections and piping to start up the pumps. The advantage for the cement plant is that the entire system is designed such that the pumps have all the beneficial auxiliaries on the skid to provide the most optimal conditions for the pumps, enhancing pump performance, reducing accidental installation risks and improving pump lifetime.
Two high-quality pinch valves utilised in dense phase system for conveying of abrasive dry cement isolation and distribution.
Control and monitoring of an automated on/off valve
Condition-based maintenance based on advanced diagnostic data has become common practice in the process industry. Smart positioners provide a wide range of diagnostic data for control valves. What about for on/off valves? Diagnostic capabilities are available using more advanced on/off controllers that solve unique challenges through intelligent valve control. Signals to monitor and report the valve position are sent to the DCS/PLC. The position of the actuated valve is controlled when the device has an integral single or dual coil solenoid valve. Easy integration into existing control systems is possible for conventional I/O – explosion proof or intrinsically safe – as well as for AS-Interface and DeviceNet installations. Touch buttons on the module will reduce valve commissioning time. Moreover, built-in intelligence can identify the valve by tag number and flash the valve controller lights to find it from a distance.
What enables conditioned-based maintenance for on/off valves is selecting a valve controller capable of wireless diagnostics using an iOS app. This
function allows for commissioning and operation of on/off valves while in the non-communication stage with the PLC and monitoring various diagnostics during communication mode.
Another advantage is getting diagnostics for cycle count, open/close stroking time and temperature. Imagine being able to identify if a valve is stuck in mid position or finding other issues. Even logging maintenance information for review and exporting as a CVS file is possible. Maintenance can be scheduled at more effective times and unplanned downtime prevented. Now have this data readily visible on an app from a safe location. Such solutions do exist.
Operating the door to digitalization
It is easy to see how more advanced on/off valve controllers are opening the door into digitalisation of on/off applications. They provide flexible and highly reliable solutions to enable condition-based maintenance for on/off applications. A significant advantage is when the chosen device has universal adaptability. Consider the benefits of being able to standardise on a controller with universal voltage capability suitable for both single-acting/spring return and double-acting pneumatic actuators and with a rebreather capability that provides better tolerance to air contaminants. Multiply those benefits when direct actuator attachment to different actuator types/sizes is faster and simpler with a low-profile, flush-mounted interface using international VDI/VDE standards. This integrated solution results in replacing existing installations of solenoid valves and limit switches as you maintain reduced inventory through the implementation of a discrete valve controller that improves operational performance for on/off applications using condition-based maintenance.
Text by Todd Loudin. Text originally published in International Cement Review January 2024 issue.
Valmet's flow control offering for cement handling
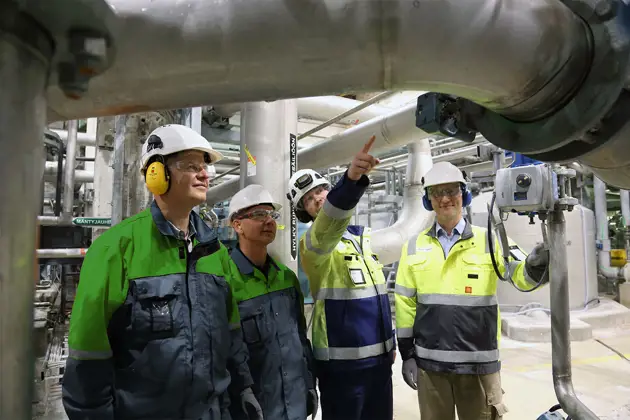
Subscribe to our newsletter
Subscribe now to flow control newsletter and receive the latest insights directly to your email.
Subscribe