International beverage company Olvi installs Valmet’s electrostatic precipitator in their Iisalmi brewery to meet emission regulations
Valmet Electrostatic Precipitator (ESP) is a cost-effective and energy-efficient solution for removing dust particles from flue gases. For Olvi Group, a Finnish-origin international beverage company, the installation of Valmet ESP brings improved reliability and performance in emission control.
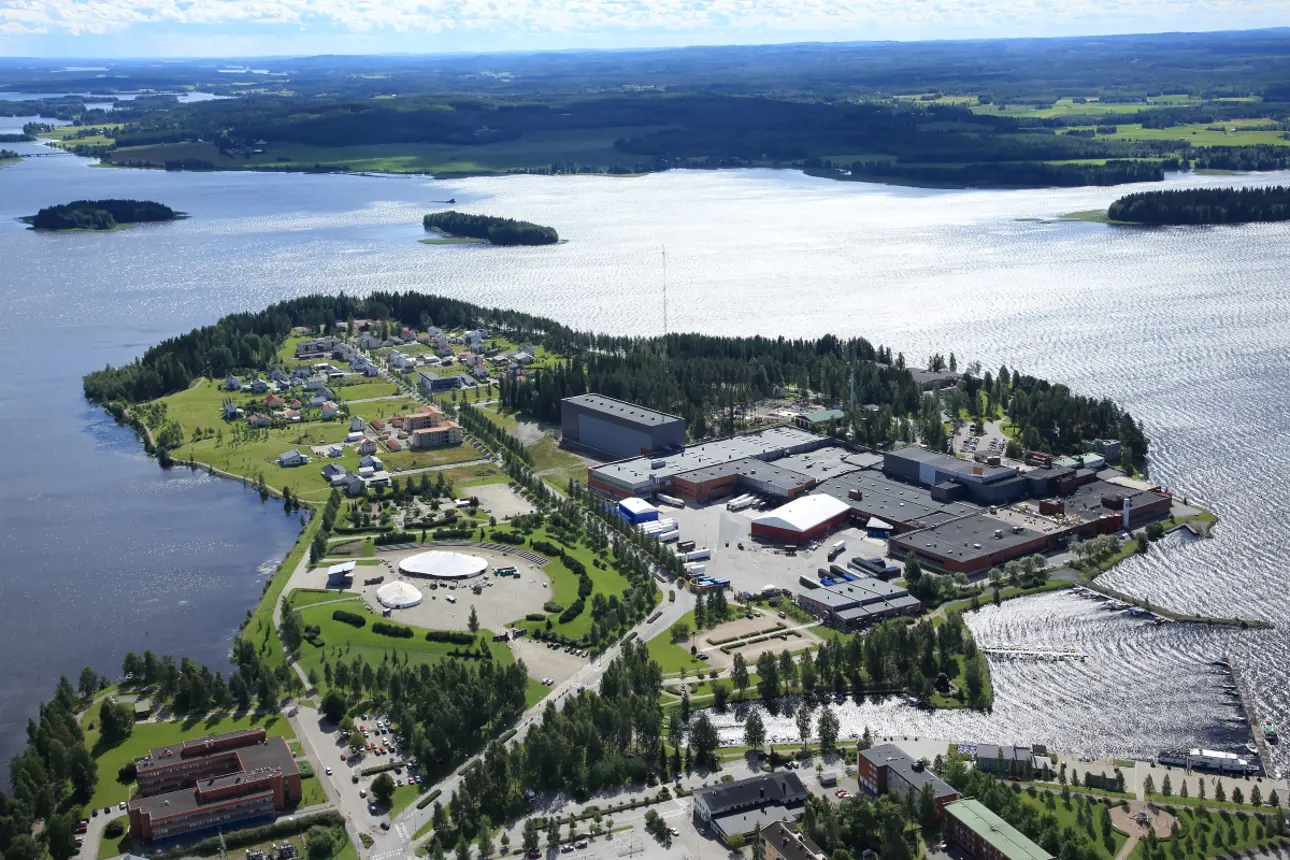
Olvi Group’s Finnish brewery is located in Iisalmi and surrounded by water.
Olvi is a Finnish beverage company established in 1878, producing one billion litres of beverages annually across various product categories, including beers, soft drinks, mineral and vitamin waters, long drinks, sports, wellness and energy drinks, ciders, and juices. Olvi operates in six different countries, with its headquarters in Iisalmi, Finland, and employs over 2,400 professionals in total.
At its Iisalmi brewery, Olvi operates a 4 MW power boiler to produce heat and steam for the factory. For flue gas cleaning and emission control, the boiler was equipped with a multicyclone.
"The multicyclone was however not working as planned, and we started to look for an alternative solution for flue gas cleaning at the Iisalmi plant. Valmet Electrostatic Precipitator was a perfect match fulfilling our needs, and we have been very satisfied with our choice,” says Jani Sirviö, Maintenance Supervisor at Olvi.
“We were convinced by Valmet’s technology, as well as by the availability of spare parts and related services,” he continues.
Reliability is the key in well-performing ESP
Valmet’s electrostatic precipitator technologies can be tailored from small scale heat plants to large recovery boilers, and they are offered as upgrades or new installations. For Olvi, Valmet delivered a small-scale ESP suitable for the customer needs and meeting the emission requirements.
“Our delivery included the engineering, manufacturing and installation of a one-field ESP together with ducting and ash conveying. In addition, we’ve supported the customer with start-up and training and will follow up the ESP performance with annual mechanical and operational inspections for an additional two years,” says Janne Katainen, Project Manager at Valmet.
The installation was completed in 2024
The cooperation and communication were on a very good level throughout the project. So far, we have been very satisfied with the new ESP. It has improved our emission control performance, lowered the pressure loss, reduced the power consumption of the fan, but most of all its reliability is excellent. The amount of maintenance breaks has practically dropped to zero,” Sirviö says.