Valmet Cutter combines safety with user-friendliness
Valmet Cutter provides the utmost safety without compromising on availability. It makes operating a cutter in a pulp drying and baling line safer, as well as more efficient and more user-friendly than ever.
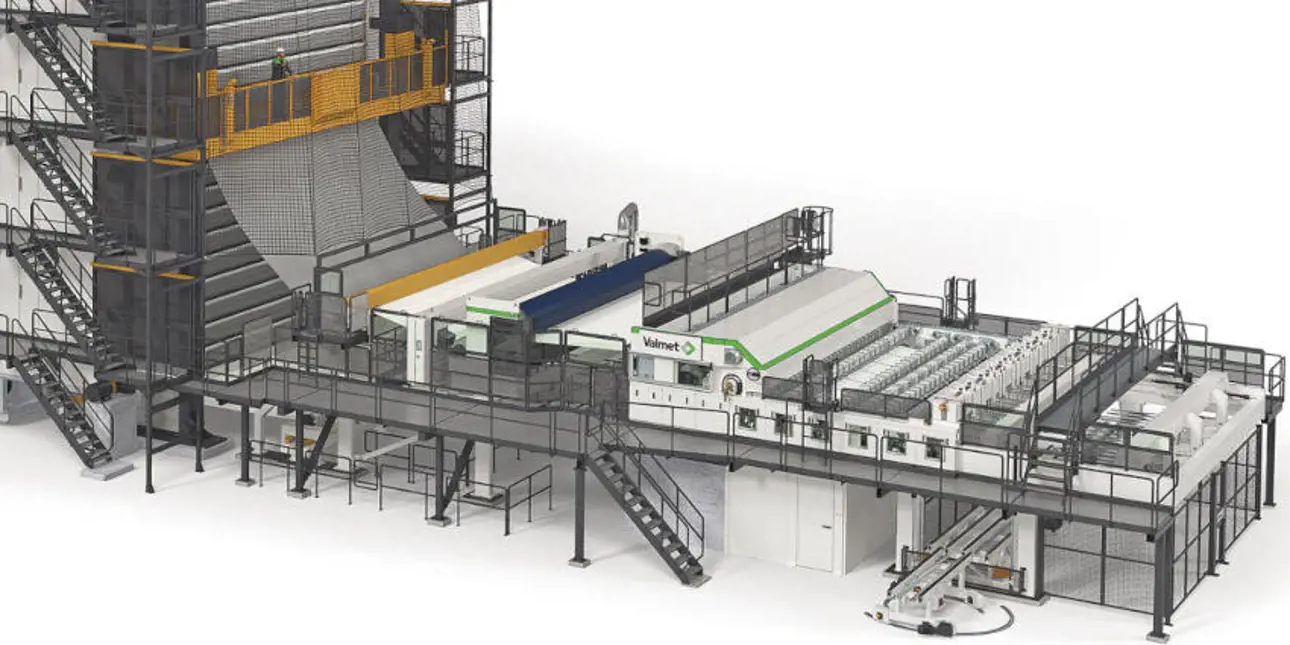
Cutters have many moving parts and often need operator attention in a pulp drying line. At the same time, cutter operation safety regulations are getting stricter around the world. Installing more safety barriers around the machine improves safety but increases the time maintenance work takes and therefore reduces productivity.
Operating Valmet Cutter is now safer than ever.
“Automating various functions makes cutter operation easier and safer. Just like our customers, we consider safety our top priority,” points out Markku Kiuru, Product Technology Manager, Cutter, Valmet. “However, we’ve kept availability in mind, while boosting safety and user-friendliness through many technical improvements. Automation enables us to maintain or exceed the earlier production speed while fully complying with the latest safety regulations.”
The Cutter Automatic Stopping System cuts the web, drops the tail into the pulper, and stops the cutter after determining the optimal stopping time.
The world’s first automatic stopping system
The Automatic Stopping System is one of the highlights of Valmet Cutter – the first of its kind in the world. It cuts the web, drops the tail into the pulper, and stops the cutter automatically. It also automatically determines the optimal stopping time based on the desired number of bale batches to be produced. If necessary, the operator in the control room can override the system and operate it manually.
“The system makes stopping safe and user-friendly, optimizes production, and increases uptime,” Kiuru says.
A redesigned cover for optimal safety
Improving safety can sometimes mean taking a step back. Valmet has removed all actuators that previously opened the cross-cutter cover; with the new design, the operator opens the cover manually with a hand wheel.
We have kept availability in mind while boosting safety and user-friendliness.
The redesigned cover is equipped with two movable parts, a liftable roof and a sliding front cover, making access to the cutting area easy and safe. This allows more space for maintenance, and the new cover design also reduces noise and creates a modern new look.
![]() |
Markku Kiuru, Cutter Product Technology Manager at Valmet, in front of the pilot cutter during a break between trials. |
Cleaning goes automatic too
Entering the cutter and cleaning it manually is always risky for operators. According to Kiuru, Valmet has minimized the need to enter the equipment by introducing an automatic clean-up concept for the cross-cutting, overlapping, and conveyor sections. The cutter cleans itself automatically after jams. If manual work is needed to complete the cleaning, the maintenance platforms make it easy. The cutter opens up, allowing more space for effective cleaning, thus reducing downtime.
Faster cutter knife change
“In addition to safety, Valmet has paid special attention to features that improve cutting process efficiency and consequently maximize production time,” Kiuru adds.
While cutter knife changes typically take 12 hours or more, Valmet has developed a two-edged turnaround cutting blade solution to speed this up, enabling changes to be made in less than eight hours – during wet end felt changes, for example. This innovative blade is installed in a clamp pocket and adjusted with the clamp pocket blade holder, and it has a fixed three-millimeter blade edge distance. Simply turning the blade around and using the other cutting edge significantly reduces downtime.
Kiuru continues: “We have received very positive feedback from our customers, who have been able to significantly extend their knife change intervals.”
Optimized slitter loading maintains optimal slitter pressure, resulting in improved cutting quality and a longer slitter lifetime.
Want to extend slitter lifetime?
Cutter slitters tend to wear out fast, especially if pressure is too high. Maintaining an optimal slitter pressure at three bar enables slitters to be precisely adjusted and improves cutting quality. Optimizing the slitter loading makes a big difference, as it extends slitter lifetime and increases uptime.
The optimal pressure is achieved with a machine automation system that drives a proportional valve. If necessary, the operator can control the slitter loading pressure manually.
Now available: Valmet Steering Roll
Steering rolls which keep the web in the line’s center have until now been supplied to Valmet Cutters by third-party vendors. To make service and improvements more available to our customers, Valmet has introduced its own automatic Valmet Steering Roll. This can be integrated with the Valmet DNA Automation System or a machine automation system.
Valmet Steering Roll ensures the pulp web’s correct alignment, if there has been any lateral web movement due to varying process conditions. “The web guide system effectively redirects the pulp web back to the cutter’s centerline, ensuring an efficient and accurate cutting process and enhanced product quality,” Kiuru says.
Stay tuned for more
These Valmet Cutter highlights represent the latest key features to improve safety, ensure availability, boost production efficiency, and increase user-friendliness. Apart from the cross-cutter cover, they are all suitable for both new equipment and upgrades.
More cutter innovations are on their way – so stay tuned!
Text: Marjaana Lehtinen
Photos and illustrations: Lars Berggren, Markku Kiuru
Valmet Cutter is suitable for all types of pulp. It efficiently cuts the pulp web and stacks the sheets into bales. Automatic features ensure maximum productivity, while complying with the highest safety standards. Key benefits for our customers include:
- Safety
- Reliability
- User-friendliness