LEIPA’s Schrobenhausen mill: Valmet Black Belt fulfills all the requirements for a high-quality shoe press belt
A high-quality shoe press belt is characterized by optimum dewatering performance, high mechanical stability, long service life and energy efficiency. At LEIPA Georg Leinfelder GmbH’s Schrobenhausen mill in Germany, Valmet Black Belt has met all the expectations.
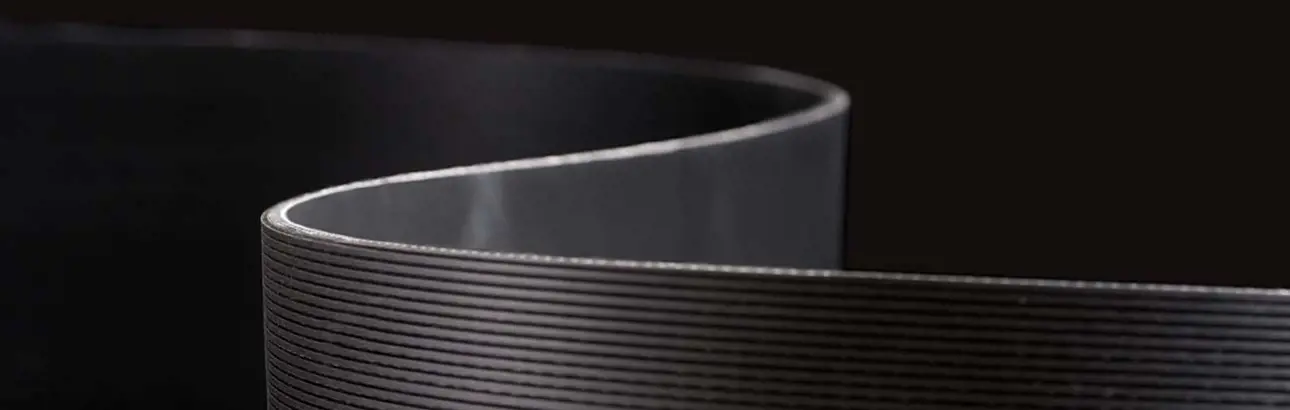
LEIPA Group is a well-known manufacturer of sustainable paper solutions with 178 years of experience. As the European market leader, LEIPA strives to convert 1,5 million tonnes of wastepaper into high-quality paper and packaging solutions every year.
Running time record of almost 1000 days with Valmet Black Belt
Valmet Black Belt is a unique shoe press belt made of high-performance elastomer material reinforced with dimensionally stable synthetic yarns. The shoe press belt is resistant to wear, chemicals and heat which ensures long and trouble-free running.
“The implementation of the Black Belt on our paper machine has been one of the highlights of our cooperation with Valmet. The belt’s performance has been confirmed in practice, and it definitely contributes to the optimization of our production process,” says Adrian Ament, Operations Engineer at LEIPA Georg Leinfelder GmbH’s Schrobenhausen mill.
“The targets we set ourselves in terms of dewatering performance, energy efficiency and durability were achieved easily. We have also ensured a stable and consistent paper quality until the end of the runtime-period of nearly 1000 days (989d), which is a new record for our board machine,” he says.
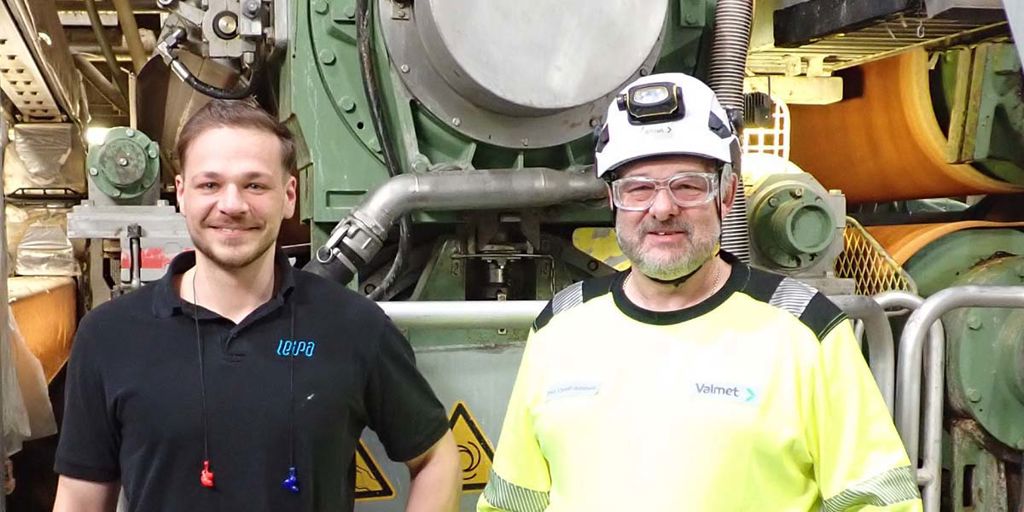
When technical expertise meets high customer service standards
To complement its full line paper machine clothing offering, Valmet provides extensive technical support both on site and remotely. The goal is always to find the optimal solution that fulfills customer needs.
“Valmet has proven to be a reliable partner with innovative solutions. We have been particularly impressed by the combination of technical expertise, high product quality and close cooperation during the entire shoe press belt implementation process,” Adrian Ament says.
“The regular exchange between Valmet and our staff and the direct support for technical questions have been particularly valuable. Valmet has not only understood our requirements but actively incorporated them into the process, and we have been able to make specific adjustments that have further increased our efficiency,” he continues.
Going forward, Schrobenhausen mill is continuously evaluating its optimization potential, particularly in energy consumption and sustainability.
“We continue to focus on sustainable innovations and efficiency improvements. The market is constantly evolving, and we want to stabilize our competitiveness with forward-looking technologies and processes. So far, the cooperation with Valmet has been extremely professional and solution-oriented, and we hope to continue the good work together,” Adrian Ament concludes.
Text: Marianne Valta