Valmet’s new low-friction doctor blades improve energy efficiency
After intensive R&D and successful customer trials, Valmet is ready to introduce a new member to the Doctor Blade family. The new sustainable low-friction doctor blades help to improve the energy efficiency at the dryer section of board and paper machines.
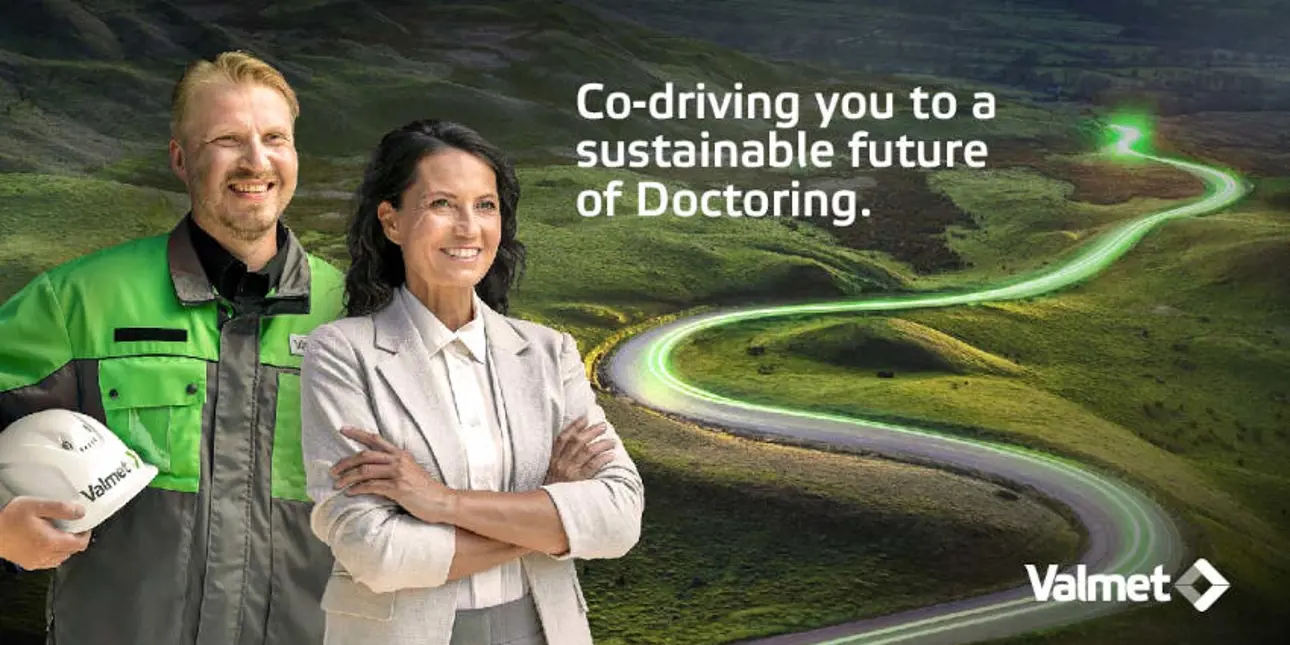
Valmet’s doctoring offering includes a complete portfolio of doctor blades, holders and accessories. Today, product development is increasingly targeted to solutions that save energy, chemicals and raw materials.
We are continuously striving to improve the sustainability of our offering either by exploring new materials for manufacturing our products or by developing features that enable our customers to diminish their environmental impact through our products. For the latter, I’m proud to introduce our new sustainable low-friction doctor blades that help to improve energy efficiency at the drying section of board and paper machines,” says Pasi Viitasalo, Global Technology Manager for paper process parts.
The new doctor blades are carbon and glass-reinforced composite blades with low-friction fillers. Their energy-saving features lead to less CO2 emissions and reduced operation costs, but the new blades also contribute to cleaner dryer cylinders and, thanks to increased blade lifetime, to less doctor blade usage.
Why low-friction blades?
About a decade ago, the Technical Research Centre of Finland (VTT) conducted a global study on energy consumption due to friction in paper machines. It showed that doctor blades’ friction represents 62% of the electricity consumption inside the drying section.
“Since then, we have developed new blade materials, run numerous friction tests and analyzed the results in order to find the optimal combination of blade material and other parameters. The performance of the glass and carbon blades has been measured against doctored surface, doctor loading pressure, blade angle, blade thickness and machine speed,” Viitasalo explains.
Significant energy savings achieved
To prepare for the launch of the new low-friction doctor blades, Valmet conducted further testing together with VTT. In the study, over twenty different blade materials were measured against friction. Following the study, trials were run at a European customer mill at the end of 2023.
In the customer trials, original blades and doctoring parameters were compared to low friction blades with original parameters and later with optimized doctoring parameters.
Based on the data given to us by the customer, the absolute electric consumption decreased by over 26% when comparing the original blades and parameters to Valmet’s low-friction blades with optimized doctoring parameters. It leads to remarkable savings in energy costs and reduced CO2 emissions. I think this is exceptional,” Viitasalo says.
The new low-friction doctor blades are suitable for all board and paper machines regardless of the original equipment manufacturer.
Sustainable low friction doctor blades
- Reduction in power consumption 26%
- Electricity savings 950 MWh/year
- CO₂ Emission reduction 190 t/y
- Annual savings 150 k€ /y