Ready to play your winning hand in tissue drying?
Imagine having a deck of powerful solutions at your fingertips, each designed to address specific aspects of your tissue machine’s drying section. With the right solutions and energy sources, you can optimize your drying process and reduce emissions.
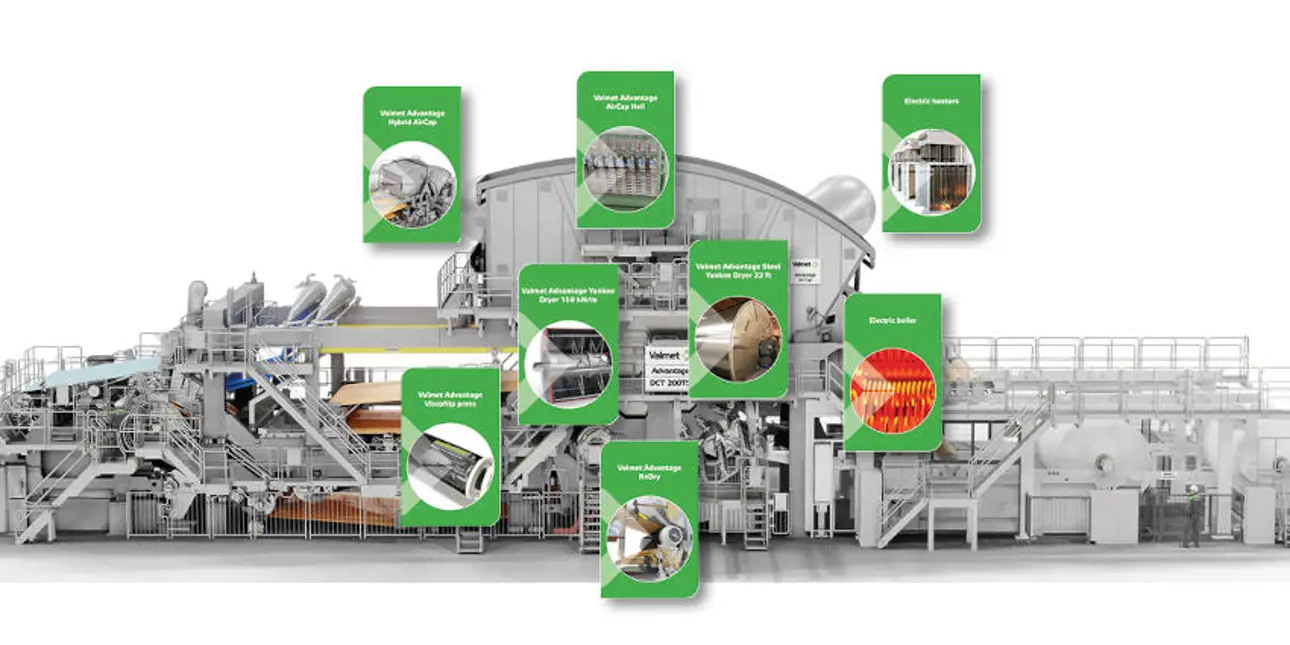
Drying accounts for approximately 70 percent of total energy consumption in tissue making, with fossil fuels like natural gas, coal, and LPG the primary energy sources. Alternative energy solutions have been developed in recent years to support decarbonization in energy-intensive industries. As tissue makers face increasing pressure to improve efficiency and reduce environmental impacts, choosing the right technology is becoming more critical. It is important to understand how to combine machinery solutions with electric heaters or hydrogen burners to meet your unique needs, whether it’s maximizing output, reducing costs, or achieving sustainability targets. But the real question is: Which cards should you play today to stay cost-effective while holding a winning hand for tomorrow?
Exploring different solutions
Valmet’s solutions are suitable for all tissue making processes, from dry crepe and hybrids to through-air drying. Several options for through-air drying machines can be explored further, including vacuum systems, advanced cleaning modules, heat recovery, and the potential to use electric heaters.
Many possible combinations are available for the Valmet Advantage™ DCT® 200 mill, from bale handling to reel. And we have some aces in our pack: Valmet’s unique industry-leading products. These include the Advantage™ ViscoNip® press, an innovative press technology which enhances dewatering efficiency, resulting in significant energy savings; the Advantage™ ReDry™, which reuses energy efficiently, boosting drying performance while minimizing energy consumption; and the patented Advantage™ AirCap™ Heli, where the headers are tilted in the cross direction, leading to uniform drying across the sheet, enhancing tissue softness and bulk while reducing energy use. These are powerful solutions, offering exceptional benefits that can set you apart from the competition.
Beyond the aces: additional opportunities
There are also other optimization opportunities. These include using a larger Yankee to increase the Yankee cylinder’s drying, which means less drying is needed on the Yankee Hood. This enables a hybrid hood with a high temperature to be included on one part, and ventilation on the other. This combination can lead to both energy and CO2 savings.
To further expand on this combination, electric heaters for the hood and electric boilers to produce steam can be added. CO2 emissions can be reduced by up to nine kg/tonnes with the first option and 224 kg/tonnes with the second expanded option. Adopting an electric heater to electrify the Yankee Hood requires no significant change in the drying philosophy because the blowing speed and temperature are kept the same.
Electric heat pump solutions are also well worth highlighting. Our studies show that using high-temperature heat pumps can significantly reduce CO2 emissions in the drying section. Traditionally, around 50 percent of the drying energy in a tissue machine comes from steam, produced by burning fuels like gas, liquid, or solids in the boiler, with efficiency ranging from 80 to 97 percent.
Drying accounts for approximately 70 percent of total energy consumption in tissue papermaking.
High-temperature heat pumps, however, are much more efficient. They recover heat from a low-temperature source, using electricity to produce a higher temperature. This process delivers more heat output than the electricity consumed, achieving efficiencies between 200 and 300 percent for steam production in tissue applications.
Holding the winning hand
With Valmet’s comprehensive selection of solutions and our experts as your strategic partners, we can help you on your journey towards zero emissions. The cards you play today may differ from those you’ll need in the future, but preparation is key. By choosing the right combination of technologies, you can optimize your tissue drying process, reduce emissions, and stay ahead of the competition.
More news and insights from the tissue industry