To remove impurities from feed gas, swing adsorption techniques have been used in industrial gas applications for decades. Today, with the emphasis on green technology and reducing emissions, these techniques are more popular than ever. Due to the criticality and inherent risks in the process, valves must be selected and manufactured to combat these challenges.
Reliable and rugged valves for swing adsorption
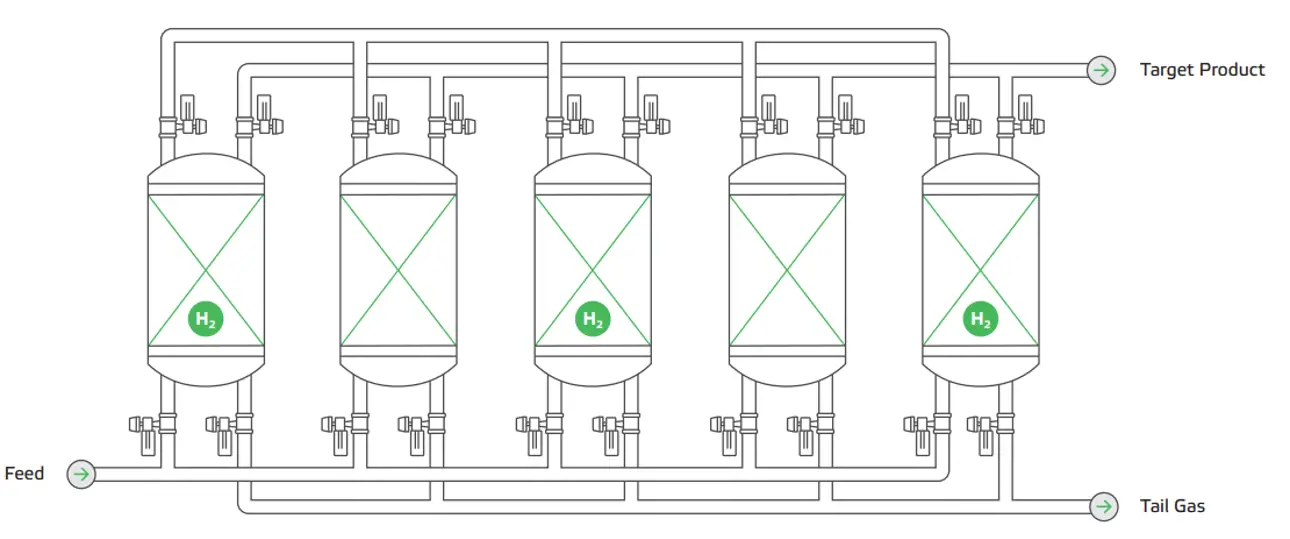
The knowledge to meet your challenges
Industrial gas technologies use various mechanisms to assist in the separation of impurities, each of which poses its own challenges to valve assemblies. Two of the mechanisms often seen are pressure swing adsorption and vacuum adsorption. Depending on the mechanism and target gas, applications may be dangerous/hazardous and require additional protection, cleaning, certifications, and more. Of course, the primary objective to the plant and end user is that processes run continuously and downtime or other interruptions are minimized.
With over 50 years of collaboration and development with our Industrial Gas customers, Valmet has the experience and know-how to meet the swing adsorption’s demanding requirements.
Demanding processes present no problem
The most common challenge for valves used in swing adsorption processes is the high cycle counts.
Valves in swing adsorption service are typically subjected to cycle times of less than 2 seconds and from 100,000 to 1,000,000 cycles per year. These valves also need to be designed to withstand highly demanding environments and abrasive media which may cause corrosion or embrittlement on installed components. Although unidirectional service is most common for the valves, bidirectional service in the case of equalization can introduce extra stress and wear on the internal components. If not properly addressed, premature failures can occur causing a halt in production until the valves can be repaired.
Other challenges include proper maintenance techniques and scheduling. To prevent unplanned downtime and reduce overall maintenance, Valmet provides specific process repair guidelines and schedules. This is also a key driver in our design to ensure that valve components are easily accessible and serviceable for a fast turnaround.
Full lifecycle reliability
As a provider of high-cycle valve solutions for decades, we use our expertise to guide our customers in their valve selection and operation over their full lifecycle. Partnering with Valmet is the ideal way to ensure long-term reduced CAPEX and OPEX through the use of reliable and efficient products. To learn more about how we can support your swing adsorption challenges, check out our Swing Adsorption application report.
Discover more on the topic
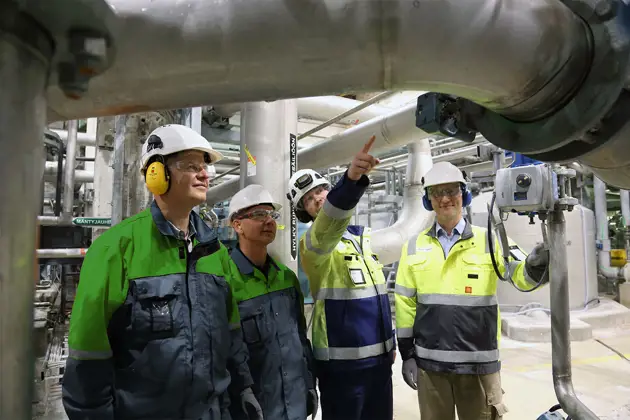
Subscribe to our newsletter
Subscribe now to flow control newsletter and receive the latest insights directly to your email.
Subscribe