Tough slurry, smarter moves: rethinking hose pumps in mining
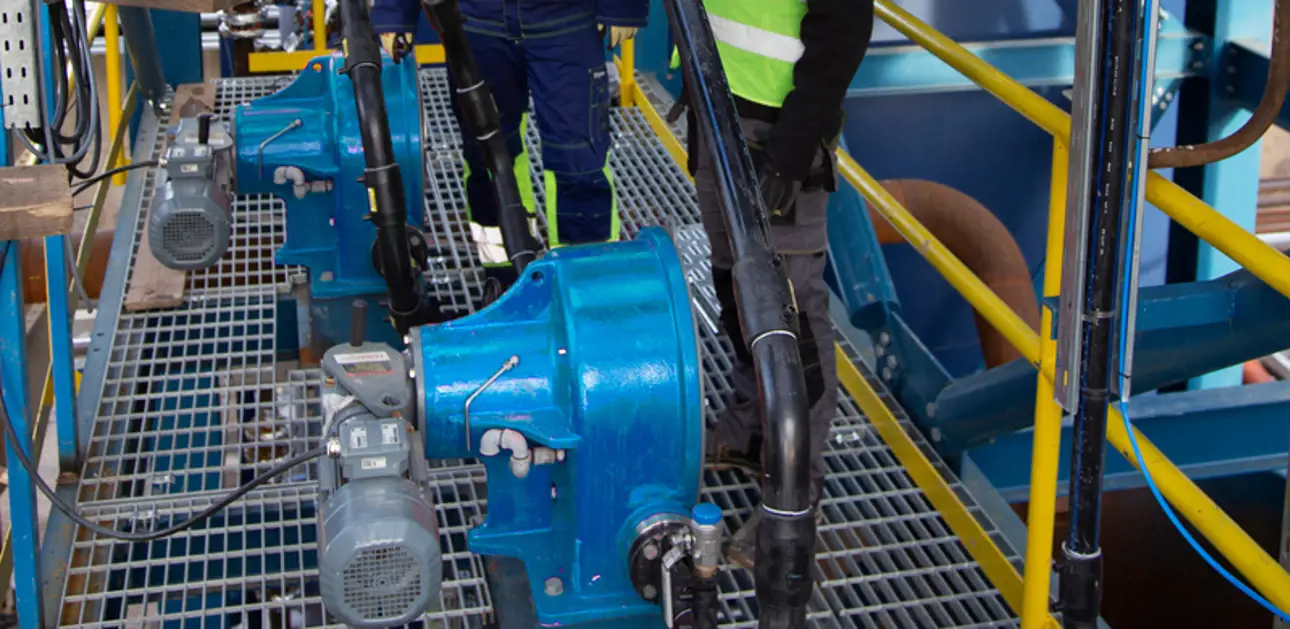
Have you ever wondered why some equipment seems to work harder, not smarter?
Mining operations are built on reliability. Every unplanned stop is a chain reaction - affecting throughput, filtration, water balance, and sometimes even safety. Pumps, often hidden in the background, are a crucial part of this puzzle. And when the media gets tough - thick slurries, abrasive tailings, chemically aggressive residues - it’s often time to consider a different approach. Valmet’s Flowrox™ peristaltic hose pumps offer more than just an alternative. They can be a shift in thinking. A move from pump-by-pump decision making to system-level reliability, maintenance simplification, and process efficiency.
One hose, one job, one point of failure
Unlike centrifugal or progressive cavity pumps, hose pumps work without seals, glands, valves, or complicated internals. A rotor compresses a flexible hose, pushing the fluid forward. That’s it.
In normal operation, the hose is the only wearing part. And that changes everything.
With Flowrox pumps, the hose isn’t an afterthought - it’s the core technology. Made with decades of development behind it, the hose is engineered for durability, pressure tolerance, and chemical resistance. And while imitation products exist, none have matched the real-world wear resistance. In many applications, customers see 3–5 times longer life compared to standard hose pump alternatives.
The role of condition monitoring
Monitoring a hose pump requires a different mindset. Traditional fast-spinning machinery - like centrifugal pumps - relies on high-frequency vibration detection, bearing resonance, and imbalance detection. Hose pumps run slowly, often below 100 rpm. The signals are softer. The faults are gradual. But they’re no less important.
Valmet has developed condition monitoring techniques tailored to the unique behavior of peristaltic pumps. The approach is not just about catching failures but understanding deviations over time.
Every new hose has a signature: a combination of vibration profile, power draw, torque behavior, and flow characteristics. As the hose wears, these signatures shift. Monitoring these shifts - especially power and torque from the VSD, and 3-axis vibration from the stator - allows maintenance teams to compare current performance to historical baselines.
It’s not a crystal ball, but over time, it becomes predictive. Changes in hose thickness, hardening, or uneven compression can be spotted before they lead to a rupture. Even process-side anomalies - such as thicker slurry, air pockets, or unexpected solids - can be detected by comparing pressure and power deviations against the baseline.
What’s more, Valmet’s system is built to be deployed locally. It doesn't need to talk to the plant DCS or cross OT firewalls. That makes installation simple, fast, and secure. For larger fleets, data can be collected to cloud services and used to benchmark pump performance across multiple sites.
Built for process, not just product
Flowrox hose pumps aren’t designed to win beauty contests. They’re more like bulldozers - slow, strong, and consistent. And they’re at their best where other pump types struggle.
Take thickener underflow. This stage benefits from pumping as dense a slurry as possible toward filtration. A centrifugal pump, even when oversized, often needs dilution to keep the flow going. That means more water into the system, which adds load to filtration, increases reagent usage, and fills up tailings pipelines faster.
A hose pump doesn’t need dilution. It can run high solids - 60 to 80% - without losing flow. In one case, switching to hose pumps halved the thickener fill time and eliminated the need for gland water. More throughput, less complexity.
Or consider tailings and sump pumping, where pump dry-run tolerance and reversibility are critical. These are chaotic points in the process. Blockages happen. Reversing the pump quickly without damaging it can mean avoiding an hours-long shutdown. Hose pumps shine here - capable of running dry and reversing flow without internal damage.
Another good example is chemical slurry feed to pressure filters. With consistent pulsation-dampened flow, hose pumps can improve filter cycle times and reduce maintenance at the filter inlet. The smoother the pressure feed, the less mechanical stress on filter membranes, connectors, and actuators.
Small details, big impact
No matter how good the design is, success still depends on using the pump correctly. A few often-overlooked details make a major difference:
After a hose break, internal cleaning is critical. If slurry residue is left inside the pump casing, it acts like sandpaper against the new hose. Even a perfectly selected hose will fail prematurely if exposed to hardened solids or dry friction from the previous break.
Likewise, tension adjustment matters. The patented compression adjustment system of Flowrox LPP-T pumps allows you to reset the compression level after hose replacement - optimizing pressure delivery while minimizing over-compression, which is a common cause of wear in less adjustable systems.
And, of course, hose material selection is everything. Not just chemical compatibility, but understanding particle shape, SG, flow rate, and even the ambient maintenance routine. Valmet specialists often work closely with customer teams to gather process data before recommending a hose type. It's the only way to match hose life expectations to real conditions.
More than the pump
Choosing a better pump isn't just about the pump. It’s about simplifying everything around it.
• No seal water? One less system to maintain.
• Dry-run capable? Fewer emergency shutdowns.
• Higher solids tolerance? Less dilution and faster dewatering.
• Self-priming? Easier commissioning and fewer airlock headaches.
• Longer hose life? Fewer interventions, fewer spares to stock.
• Local condition monitoring? Easier planning, no surprises.
In mining, small improvements stack up. Over a year, a small change in pump type can ripple through operations - reducing water use, cutting downtime, and making planning easier for maintenance teams. That’s the quiet power of a well-executed hose pump strategy.
Text by Simo Rounela. Originally published in the Pump Industry digital magazine.
Read more related articles
Flow control for different applications in mining, metals and steel