Defibrator system
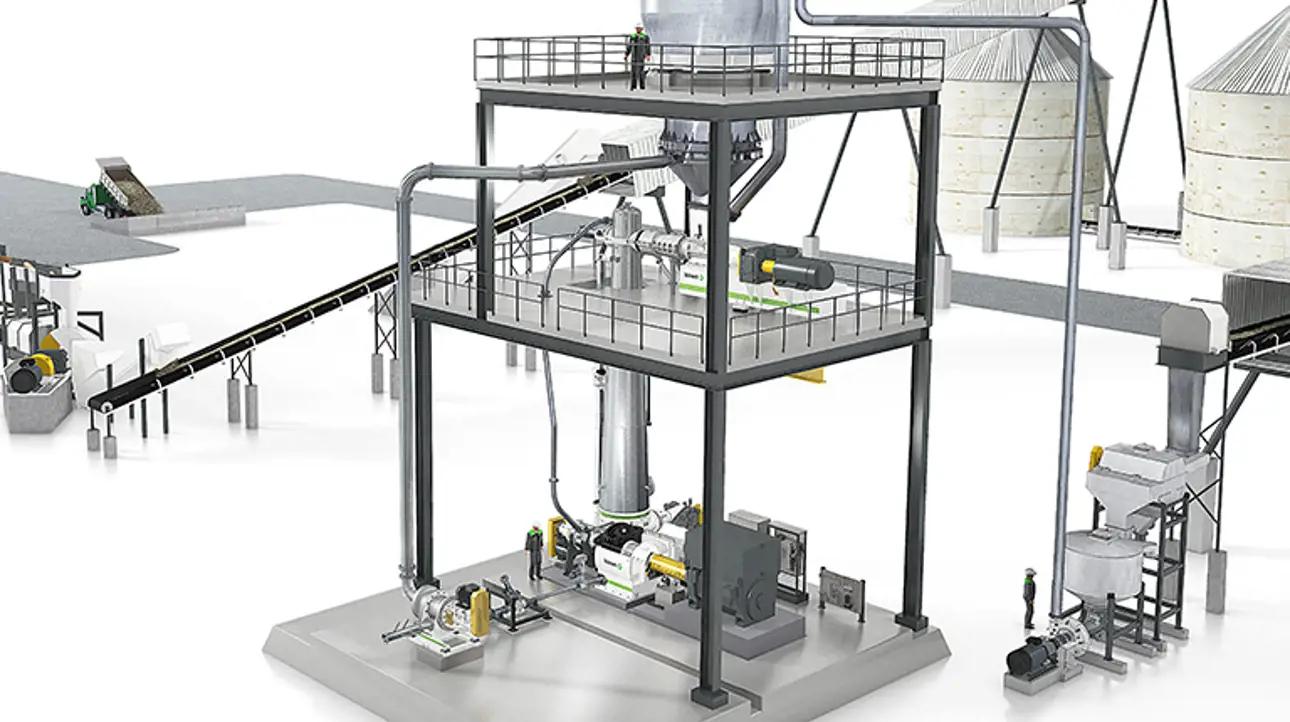
Fiberboard producers turn raw materials, such as wood chips or wood waste, into durable consumer goods and commercial products, that range from flooring to furniture. Manufacturing medium-density fiberboard (MDF), insulation board or other fiberboard products, requires a fiber processing system, which in Valmet is sold under the name Valmet EVO Defibrator System.
Low operating cost
Low energy consumption
Excellent dewatering capacity
Minimal water consumption
Through extensive research and development, Valmet strives to be the technology leader and the benchmark, within the industry offering sustainable solutions, that customers can trust to help them achieve their goals. Great efforts are made to prioritize equipment reliability, reduce production and maintenance costs, and deliver the most environmentally friendly solutions.
Introducing the Valmet Defibrator System
The unique fiber processing system from Valmet is designed to help fiberboard producers lower operating costs, reduce energy consumption, reduce maintenance costs, and extend the lifetime of equipment and components.

Chip bin
The chip bin acts as a buffer and it will also heat the chips with steam and secure good feeding of the raw material to the plug screw feeder. Valmet have developed a new type of chip bin to secure even and effective heating of the chips as well as provide good feeding to the plug screw feeder. Valmet chip bin's is also suitable to handle recovered steam coming from e.g the steam separator.
Raw material like wood waste requires an active feeding bin, like the Valmet Chip Bin DB
Plug screw feeder
The plug screw feeder feeds the raw material, into a pressurized preheater (or digester). The feeder should remove as much water, together with extractives as possible. This is the key to reduce production costs like steam consumption, dryer energy as well as environmental impact by reducing V-O-C emissions in the dryer.
Valmet plug screw feeders are made of cast heavy-duty parts, to ensure the longest possible lifetime and reliability. Extensive live trials and computer simulations in our Fiber Technology Center have been key success factors, in ensuring that the plug screw feeders, were developed with the highest dewatering capacity in the industry. By removing 5% more water than any competitor feeder.
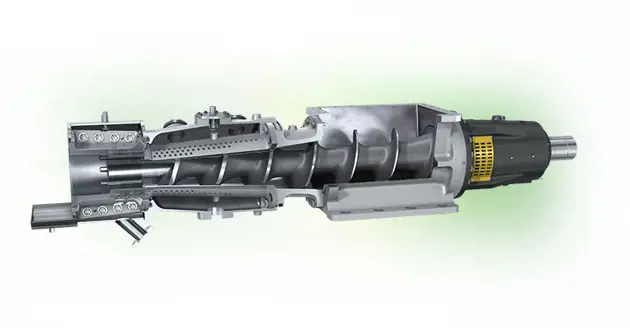
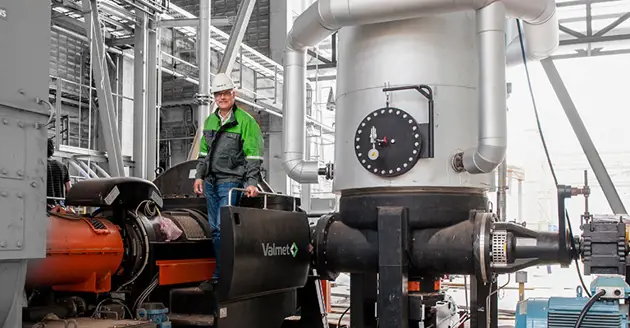
Preheater, the enabler for smooth refiner operation at low energy
The preheater heats the raw material with pressurized steam, to soften the lignin and reach desired fiber quality in the refiner.
For smooth refiner operation at low energy – Valmet preheater has a discharge screw with a compression zone.
This compression zone is an important detail – that distinguishes Valmet's design from other solutions on the market. Also helping the equipment stand out – is its durability and reliability. The Valmet Preheater is usually cast in a thick material for long life
Minimum water to the process with Valmet Mechanical Seals
To minimize the environmental impact Valmet has developed a new mechanical sealing system including double cartridge mechanical seals and closed loop water system which minimizes the water that enters the process. With this function you save fresh and waste water which results in reduced water costs and thermal energy savings due to less water to evaporate in the dryer.
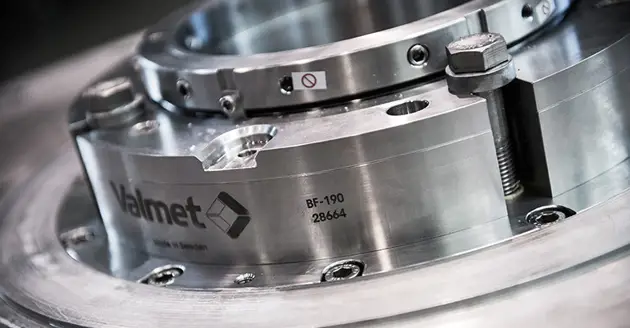
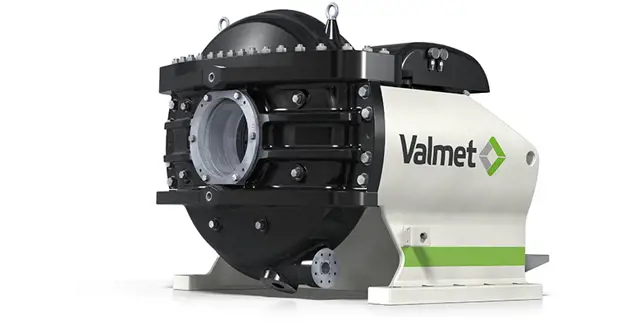
Energy efficient separation of fibers
Valmet EVO Defibrator is the most innovative and cost-effective defibrator in the market. The refiner or Defibrator – grinds the raw material into fibers. For energy efficient separation of fibers, the refiner must be rigid, and the grinding segments must be parallel under all different pressures and production conditions.
A patented second-generation grinding disc housing – and stand – is now available for Valmet Defibrator. Manufactured with thick cast-parts, the patented housing has undergone thorough computer simulations, as well as full-scale tests, that show energy and resin consumption savings of up to 10%.
Full range of tailored production consumables
Valmet offers a wide range of consumables to optimize your mills performance, making the most out of the least. Choosing Valmet as a supplier provides long consumable lifetime and lowest possible costs. Our consumable agreements are always individually tailored for each production line.
Valmet has a strong tradition in developing new product families for Refiner Segments. Since the introduction of Attack bar in 2005, features like Turbine segments, Equal lock and more recently Vacuum flow and Pitch clean has been rolled out.
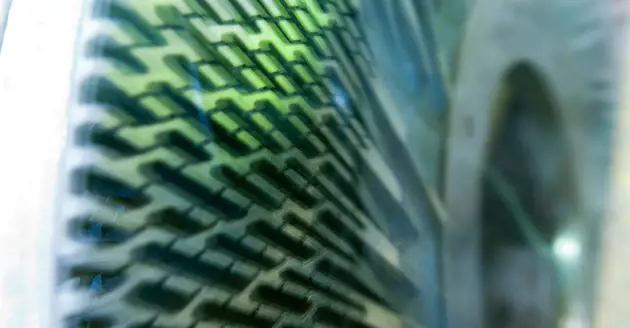
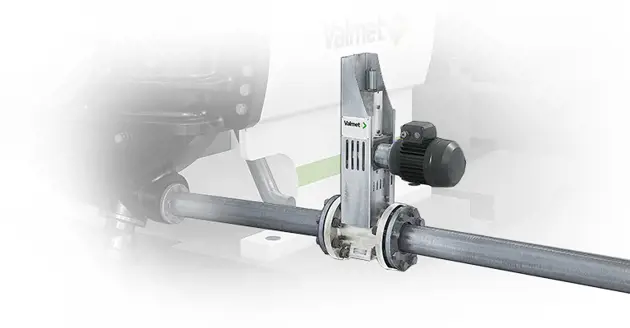
Wear resistant blow valve
Valmet’s generation 2 Defibrator system – has a new patented blow valve – that further stabilizes the process, and features thick, easily replaceable wear sleeves.
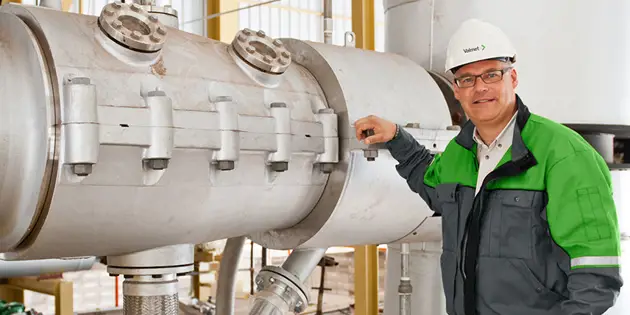
Our expertise is at your service
Our focus is to bring your performance forward utilizing our extensive experience and in-depth knowledge of pulp process technology. Get in touch with our experts through your local Valmet office, or the link below.
Contact uskeyboard_arrow_leftBack
{{currentHeading}}
{{productForm.Name}} {{"("+productForm.Size+")"}}